In the realm of construction and woodworking,
the humble iron nail plays a pivotal role. The iron nail, a small yet essential tool, is celebrated for its reliability and strength, remaining a staple in the industry for centuries. As the demand for construction and manufacturing surges globally, the iron nail industry is more critical now than ever before.
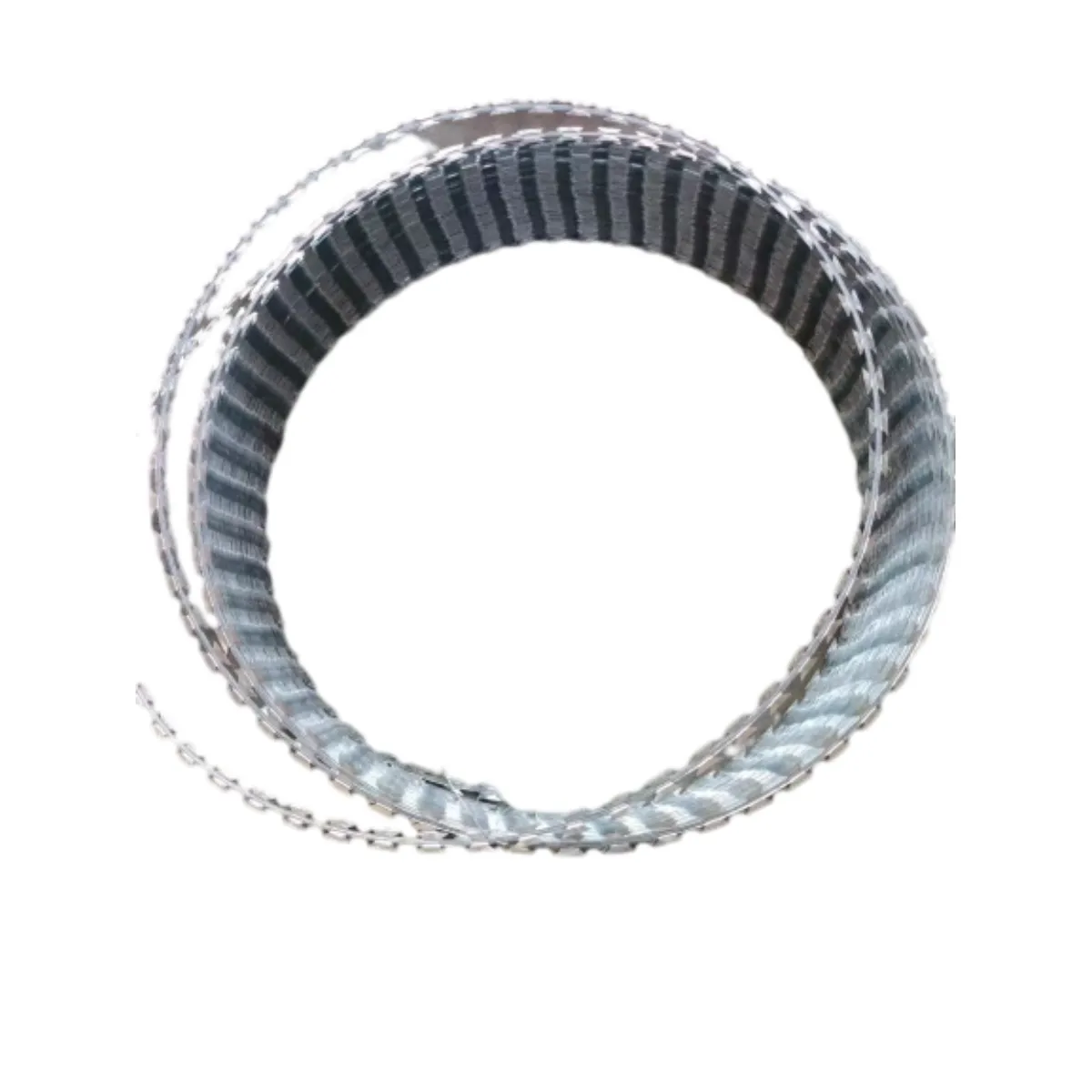
The production process of iron nails begins with the careful selection of raw materials, specifically iron wire rods, which are the primary source of iron. The quality of these rods directly impacts the durability and effectiveness of the final nail product. Reputable manufacturers source these rods from trusted suppliers, ensuring each batch meets strict quality standards, thereby providing a solid foundation for subsequent production stages.
Advanced machinery plays an integral role in transforming raw iron into perfectly sized nails. Automated wire drawing machines are employed to achieve the desired thickness, pulling the iron rods through a series of progressively smaller dies. This step demands precision and expertise, as the consistency in thickness ensures uniformity in the production process, directly affecting the nails' usability and strength.
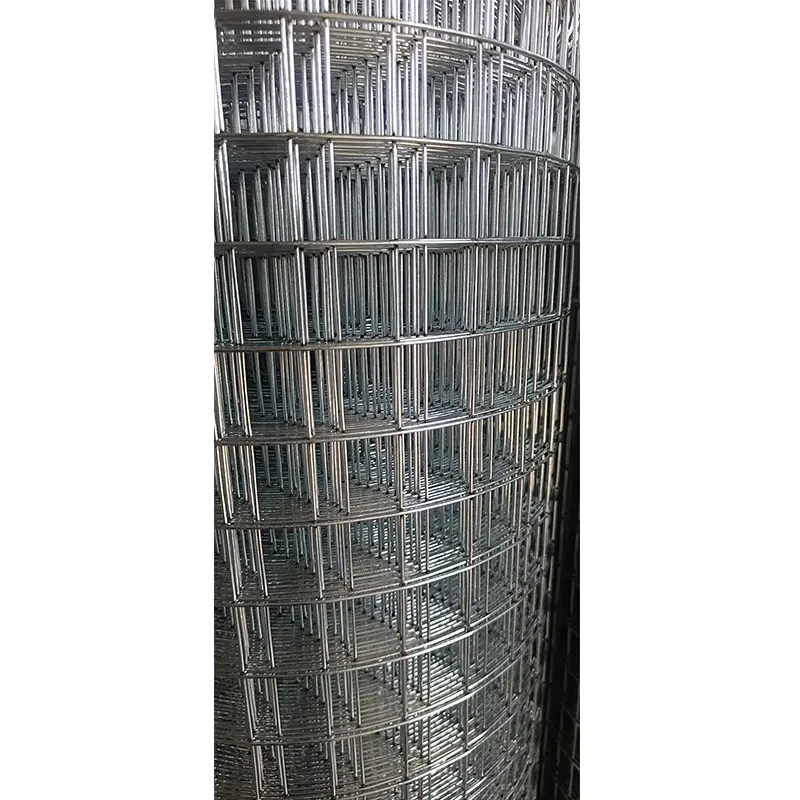
The next critical step is cutting, where the drawn wire is segmented into specific lengths according to nail specifications. Here, expertise is vital; manufacturers utilize cutting-edge technology to ensure each cut is exact, minimizing waste and enhancing production efficiency. The precise cutting process is fundamental, as any discrepancies can lead to compromised structural integrity.
Following the cutting stage, the nail heads are formed through a process called “headering.” This involves compressing one end of the cut wire to form the head of the nail, an area that requires durability to withstand driving into various materials. This step is executed with expert knowledge and meticulous attention to detail, ensuring each nail head is formed with the strength needed for high-performance applications.
iron nail manufacture
The process of sharpening the opposite end of the nail, known as “pointing,” requires finesse and control. Expert machinists ensure the tip of each nail is sharpened to perfection, designed to penetrate materials with ease and accuracy. A well-pointed nail reduces the effort required for manual or machine hammering, enhancing ease of use and efficiency.
After the nails are forged, heat treatment processes are applied to boost their resilience. Experts in metallurgical engineering oversee treatments such as annealing and quenching, which alter the nail’s microstructure, enhancing its hardness and preventing brittleness. The expertise applied during this stage significantly increases the nail's lifespan and performance, validating the manufacturer's authority as a leader in quality nail production.
Finally, surface treatment, typically involving galvanization, ensures nails are rust-resistant, extending their longevity. This additional layer of protection is crucial, especially for nails used in outdoor constructions exposed to the elements. Trustworthiness in the construction industry often hinges on such details, where a nail’s ability to resist corrosion can determine the success of a project.
Iron nail manufacturers embrace cutting-edge technology and adopt rigorous quality control measures to meet industry standards. This commitment to excellence and reliability solidifies their position as leaders in the field, offering clients products that boast both expertise and a track record of dependability.
In conclusion, the iron nail manufacturing process is steeped in expertise, from the selection of superior raw materials to meticulous forging and finishing techniques. Manufacturers committed to maintaining high standards of authoritativeness and trustworthiness continue to thrive, delivering essential products that underpin countless construction projects around the world. Each nail produced stands testament to the skill and dedication embedded in the industry, reinforcing the essential role of iron nails in modern construction and beyond.